Solar shading manufacturer Verosol is experiencing rapid growth, and currently training a new generation of operators with EZ-GO. In addition, the company is facilitating autonomous maintenance and continuously improving production processes.
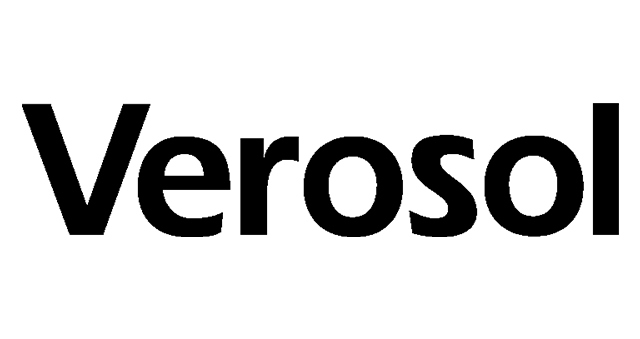
‘When I ask my children how to do something, they refer me to YouTube’ says Detmar Roessink, CEO at Verosol. ”The paper world is not the way of the future. You can never explain something as clearly on paper as you can with videos and photos. Which is why, when we were looking for a solution to schedule autonomous maintenance and transfer know-how, we knew it had to be in digital and visual form.’
Transferring know-how
Verosol manufactures solar shading products. The weaving of the cloth, metallisation of the fabric and assembly into complete solar shading products all take place at our own locations. ‘We are a genuine craft firm,’ continues Detmar. ‘Our experienced employees have a lot of know-how, and their average age is high. Right now, we’re experiencing rapid growth, so lots of new, young people are joining us. However, we didn’t really have any proper training material to deal with this influx. With EZ-GO, we have found an excellent solution.’
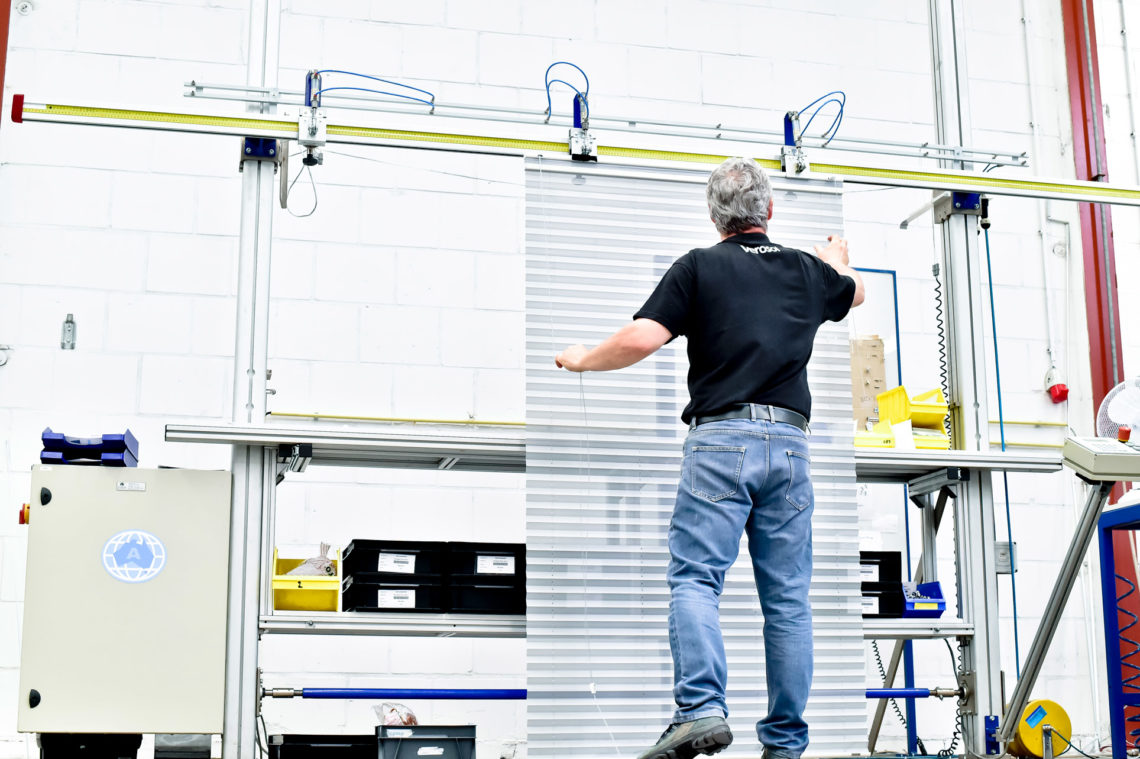
Organising autonomous maintenance
Another important reason to start working with the platform is that there was little structure to scheduled activities such as cleaning, inspection and maintenance. Detmar: ‘I am really someone of the TPM school (Total Productive Maintenance), and believe in autonomous maintenance by the operator. But this is something you have to facilitate. This platform also provides the opportunities for it.’
“I am really someone of the TPM school (Total Productive Maintenance), and believe in autonomous maintenance by the operator. But this is something you have to facilitate. This platform also provides the opportunities for it.”
Detmar Roessink
Director Production Verosol
Phased introduction
In the Netherlands, Verosol/Kvadrat has three production sites: for weaving, metallising and assembly respectively. The implementation of EZ-GO at these locations is led by Kilian Bennink, as part of his role as Supply Chain Manager. ‘In March 2021, we commenced operations at the plant where we metallise fabrics. These are batch processes with rolls of fabric of up to 4,000 metres. The existing work instructions hadn’t been revised for a long time – with many not recorded at all -, so we started with these. We began by looking at the two most complex machines. After revising the work instructions, the actual filling of the app with text and images required very little subsequent work. For these machines, everything took two days. This was followed by the roll-out to the other machines and the use of more functionalities from EZ-GO. We also include 5S audits in the app, for example.’
The other locations followed. At each location, the project leader initially gives a presentation to show what the EZ-GO platform entails, and how it can be of use to the operators. The project team organising the implementation always includes a team leader and some operators. After all, they know the processes and, most importantly, exceptions. Kilian’s role is diminishing with each location, he says: ‘I am currently training someone to manage the project at the weaving mill.’ Implementation will start there in December 2021.
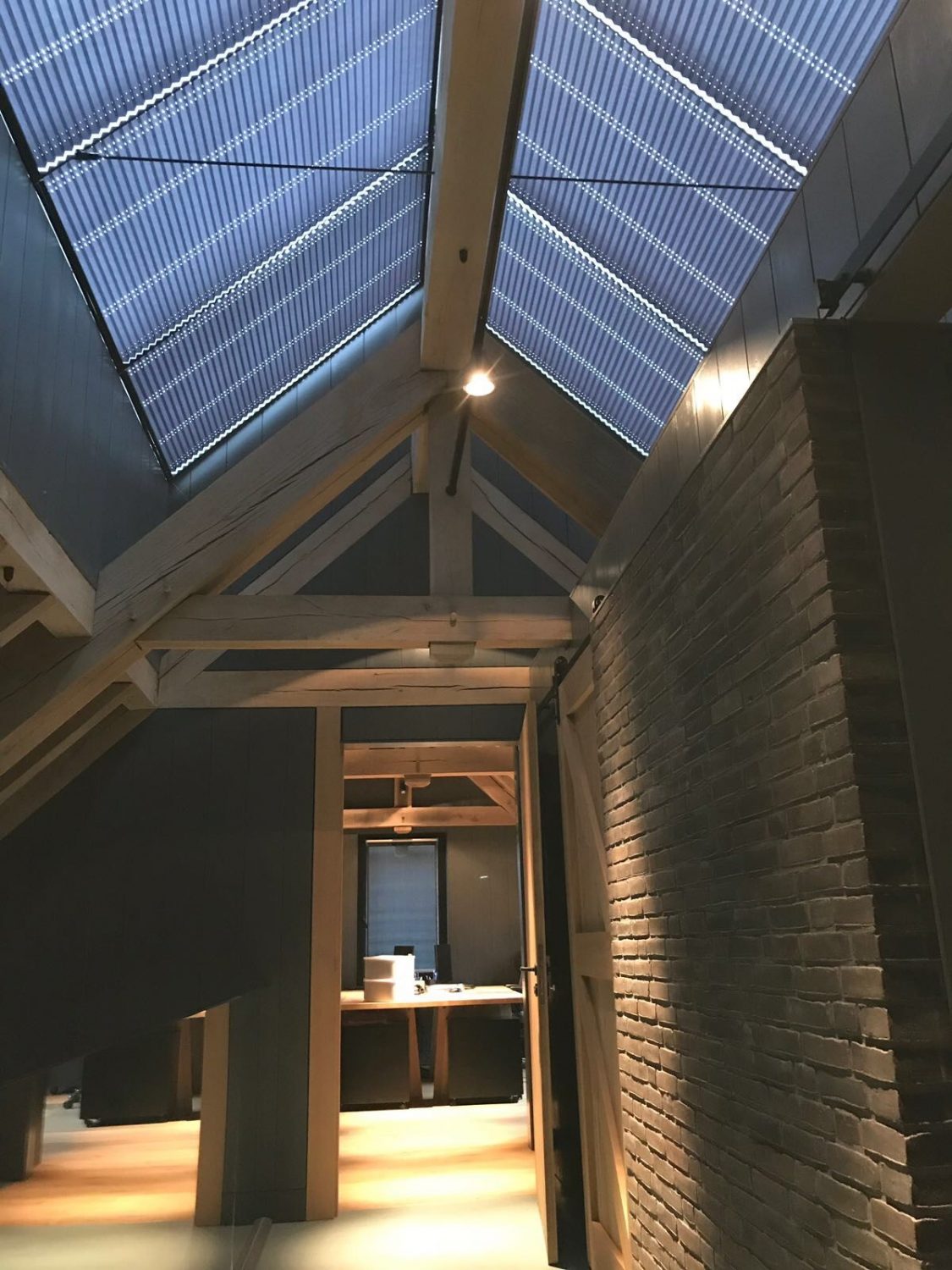
Training with the app
GEMA started working with EZ-GO in October 2021. ‘In the beginning, things went quite quickly,’ says Rudi. ‘We started with a small department, sat down together and filled the app with the employees. Now we are rolling it out to other departments and activities. It is certainly not my intention to fill in everything. EZ-GO is so great because employees can put in the necessary information themselves. Marco and I mainly have to create the framework and give the employees time for it, for example by giving them a day off now and then from their daily work. Which means it’s done in no time. We expect to be completely finished with implementation by summer 2022.’
Results
So, although GEMA is still busy with implementation, they already see follow-up possibilities. Marco: ‘For example, we want to start using the checklists we ourselves use for projects when handing over to the client. I also see possibilities for new applications. With energy prices nowadays, why not make an energy-saving checklist? Everything is possible. That’s because EZ-GO contains basic templates that you can easily set up to meet your own requirements. What’s more, it is easy to change the current lists and tasks if working methods change or if, for example, a new machine is introduced. The possibilities are endless.’
Ready for the future
It is no coincidence that Verosol is currently undergoing this professionalisation process. The company is moving fast. After long-term ownership in the hands of an investment company, it has been part of a committed Danish parent company since 2019. From July 1, Verosol’s name will change to Kvadrat. ‘We are now really catching up with investing in people and production capacity,’ says Detmar. ‘It is certainly difficult to find people in the current labour market, so thorough education and training is extremely important for us.’
Verosol currently equips all Booking.com office buildings with solar shades; at the same time, it is engaged in numerous other large projects, and also serves the retail market. Which means you need to get things right. There’s no issue on that front, confirms Detmar. ‘The learning capacity of this system was an important reason for us to opt for EZ-GO. We can measure the safety, quality and speed of processes, and adjust where necessary. If new products and processes emerge, we can easily add them. And everyone can work with them.’