For years, Aviko Rixona has been looking for a user-friendly and simple system for the digitisation of work instructions, checklists and audits. ‘Paper is a thing of the past,’ according to production manager Jimi Aarts. As it turns out, EZ-GO is the solution. The first line is fully operational by May 2021, a year later all factory and packaging lines will be digitised. Together with operator Michael van Keulen and performance coordinator Stef Heerkens, Jimi explains how it is done.
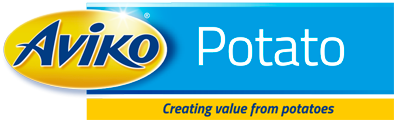
Aviko Rixona produces potato flakes and granulate for the fast-food industry, among others. The company had been looking for an alternative to their paper-based work instructions and checklists for a while, according to production manager Jimi Aarts (plant manager since 1 July 2021): ‘We used to work with a 30-page document containing all cleaning and inspection tasks. Operators would tick the boxes in hard-copy lists. It was cumbersome, unclear and old-fashioned. Still, it took a while for us to find a good digital solution. Some providers made it too simplistic, others too complex. EZ-GO offers just the right level of user-friendliness and flexibility for us.’
Selecting a compact line
For the implementation, the Limburg-based factory opted for a factory line that allows for proper testing of all functionalities. Operator Michael is part of the project team. He clarifies the decision: ‘Line 6 produces potato flakes, making it a true process line. Plus, this is where a lot of new and young operators work, the line is limited to a single space and the process is transparent. Perfect to kick things off with.’ Stef Heerkens is in charge as the project lead and makes up a team together with Michael, team lead Suat and quality controller Marie-José. Their schedules have been freed up for this initial implementation, allowing them to dedicate themselves completely. EZ Factory’s Martijn Brussen and Robert Bouwman assist with on-site preparations.
As it turns out, the implementation of the app is a great moment to review the old material, according to Stef: ‘Departing from the paper-based tome, we updated all tasks, procedures and checklists and made new photos of everything.’ Michael adds: ‘We also subdivided tasks into smaller pieces: where a single task may have contained several steps in the past, they have now been entered into EZ-GO step-by-step. Plus, we made instruction videos that have proven very useful because they show the operator what to do at a glance.’ Jimi smiles: ‘In theory, I can now operate the entire line using EZ-GO. I’m not even kidding: thanks to EZ-GO, new employees can get started right away. It appeals to younger employees in particular, but our seniors know their way around it just as well by now. We conducted a survey among the operators at line 6. They rated the app a 4.5 out of 5 and were especially pleased about the user-friendliness.’
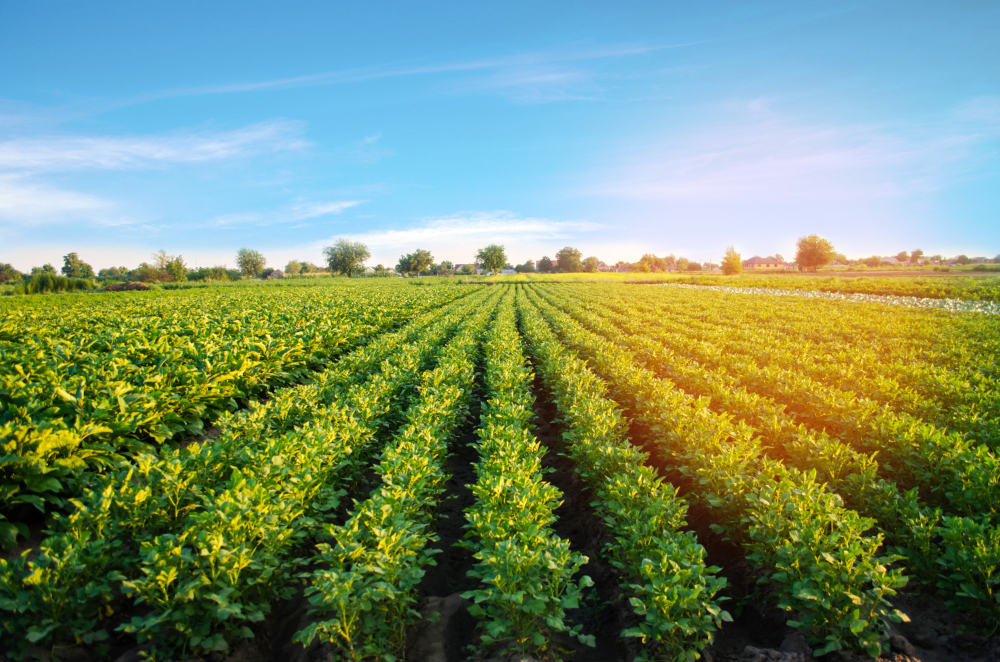
Well begun is half done
After a good preparation, it is relatively easy to enter the material into the app. Stef booked the project team for a week to get it done. ‘The first day was more difficult than we had hoped, one issue was that our photos weren’t as good as we thought. By midday, we had only entered three tasks. But once we got the hang of it, we managed to pick up pace and by Friday, everything was done according to schedule.’
In May 2021, the team gave the app a positive assessment on line 6, and Aviko Rixona is exceedingly likely to implement EZ-GO throughout. Stef boasts: ‘We want the app to contain all lines by the summer of 2022, both for processing and for the filling department. The most time-consuming aspect will be to update procedures and checklists. After a good preparation, it is relatively easy to enter everything into EZ-GO. The team leaders and operators will be conducting the implementation on their own, parallel to their regular work. I will be overseeing the process while kicking off the implementation in our other Dutch factory.’
“EZ-GO is easier, more transparent and more fun to work with, and it improves productivity by keeping the workplace tidier and ensuring that actions are followed up on more quickly and effectively.”
Michael
Operator Aviko Rixona
Improvement through use and reports
The company has a very loyal workforce with a huge amount of experience and knowledge. Some of them will retire in the years ahead. How does one effectively transfer all of that knowledge? Wim Rutten: ‘Once again, EZ-GO proves a perfect solution. Work instructions with photos and videos are clear, unambiguous and great for training new staff. We also use EZ-GO to create tasks for managers, allowing them to test what skills employees possess and what they still need to brush up on.’
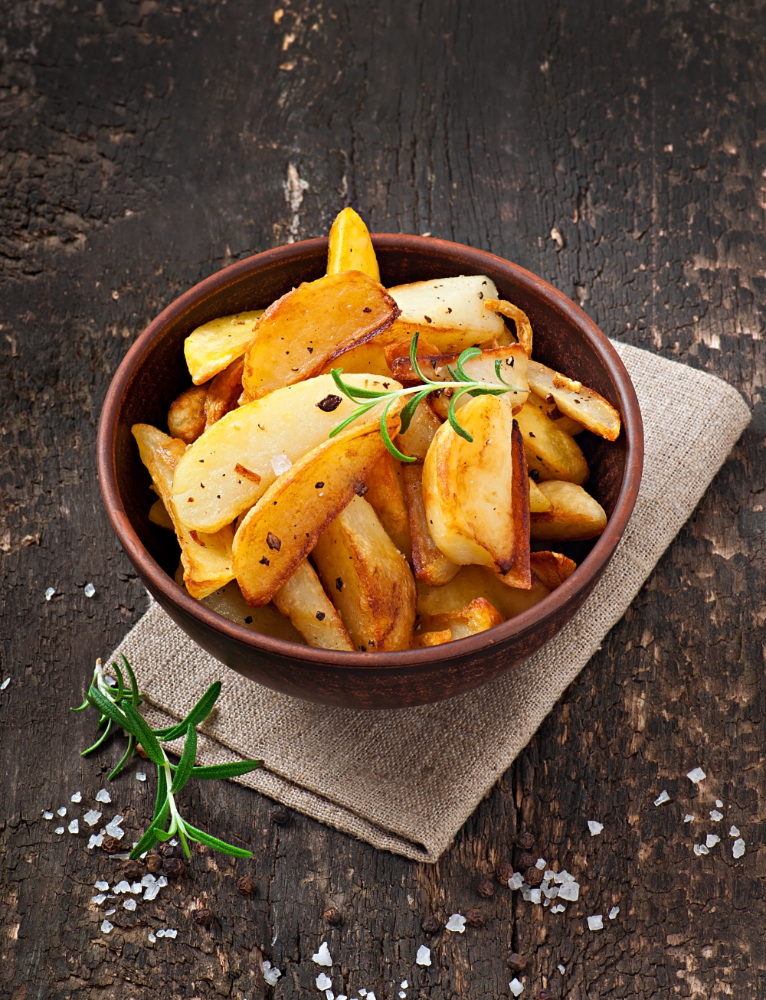
Easy to create actions
The operators love the ability to create actions in the app. Adding a photo, being kept up-to-date on the status and ticking the box on an action when done; all very useful. When a notification is intended for the technical service, the team leader uses the existing system for deviations to forward the message. The two systems can’t replace each other but they do operate in concert. They would like them to be connected in the future. In the first months, forty actions were entered and 80% was followed up on.
Faster and better audits
So far, Aviko Rixona entered two audits into EZ-GO; the GMP (Good Manufacturing Practice) and the glass audit. Both are conducted every five weeks via the app, which makes them a lot more user-friendly than before. Plus, providing information in the event of external audits becomes a lot easier too, according to Stef. ‘External auditors have their own checklists, of course, but it is now very easy for us to demonstrate, based on the app, that certain things are in order. All it takes is one tap of a button to demonstrate our everyday inspection and cleaning, for example. And historic information is easy to pull up as well.’
Ready for new operators and new machines
The next major step will be to implement audits. At the moment, it still takes a lot of time to conduct, register and follow up on audits. This is where Thijs Moorthamer expects the most efficiency gains to be made. ‘Once again, we will work in two stages: first, revising the audit and arranging it more logically, e.g. by increasing the distinction between 5S-like tasks and more weighty things that require less frequent auditing. In addition, I expect more time gains because of the fact that audits will be digitally recorded in EZ-GO directly, and actions assigned in real time. No more copy-pasting, uploading photos or mailing actions. This will make a huge difference for Confiserie Napoleon.’