Uzimet is the only lead sheet manufacturer in the Benelux. Safety, quality and responsible production are paramount when processing this material —something the EZ-GO platform helps achieve, while also improving internal communication, stock management and ISO reporting.
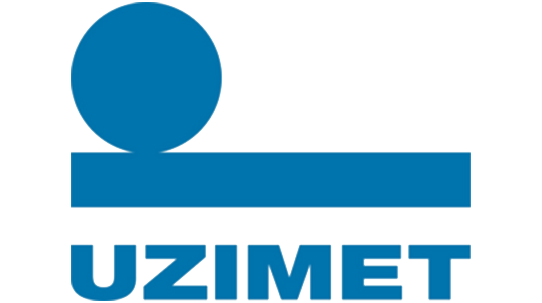
This company video demonstrates the lead processing procedure and the importance of safety. Everyone works with PPE and various types of respiratory protection, including entire hazmat suits. Operations Director Franklin Weenink explains: ‘Safety is our number-one priority. When processing lead, it’s vital to avoid inhaling dust. That’s why we have a gigantic suction machine; when that machine breaks down, the entire operation grinds to a halt. Its maintenance is mission-critical, which is why we perform lots of inspections and preventive maintenance. Each step of the lead processing procedure consists of many tasks that need to be performed daily or weekly to ensure proper operations and guarantee everyone’s health and safety. EZ-GO presents these tasks proactively, ensuring they are conducted systematically and that deviations are easy to report. This has reduced our breakdown rate, boosting productivity, quality and safety. Plus, it has ended the need for paper —a notorious propagator of dust — in the workplace.’
Checklists and actions for improvement
Uzimet opted for EZ-GO for several reasons. Firstly, it has a practical and simple setup; rather than long-winded copy, it offers simple photos that clarify what needs to be done at a glance. Secondly, it delivers a proactive approach: tasks and inspections are displayed per day rather than having to be looked up on a piece of paper. And finally, it improves communication. Weenink: ‘Every operator can report deviations or make comments in the app and forward them to the right person. Whenever a structural adjustment is required, assigning or adding a task in EZ-GO is as easy as pie.’
Production leader Akash Soochitsingh: ‘We have what we call a GO meeting every morning to discuss all interruptions and reports of the past 24 hours with the operators and staff, such as from facility management and engineering. When it comes to complex matters, we determine the right course of action in consultation. The person who reported the action is the only one who can tick it off.’ According to Weenink, this is how it should be: ‘This guarantees actual resolution of the issue.’
Faster operators
Weenink and Soochitsingh implemented the app together, which meant going through the processes, creating instructions and photos and entering them into the system. Soochitsingh: ‘One reason why that was quite a considerable task is that we used the opportunity to clean up various checklists and work instructions. But it was totally worth it. We got the rest of the team involved, of course, and trained all operators so they could create actions in EZ-GO as well. They love the app, especially because it speeds up their work. They no longer have to walk around with a pen and paper, writing down numbers and handing in lists to be typed up. Plus, you simply can’t forget a task or inspection anymore, because the app tells you exactly what needs to be done that day.’
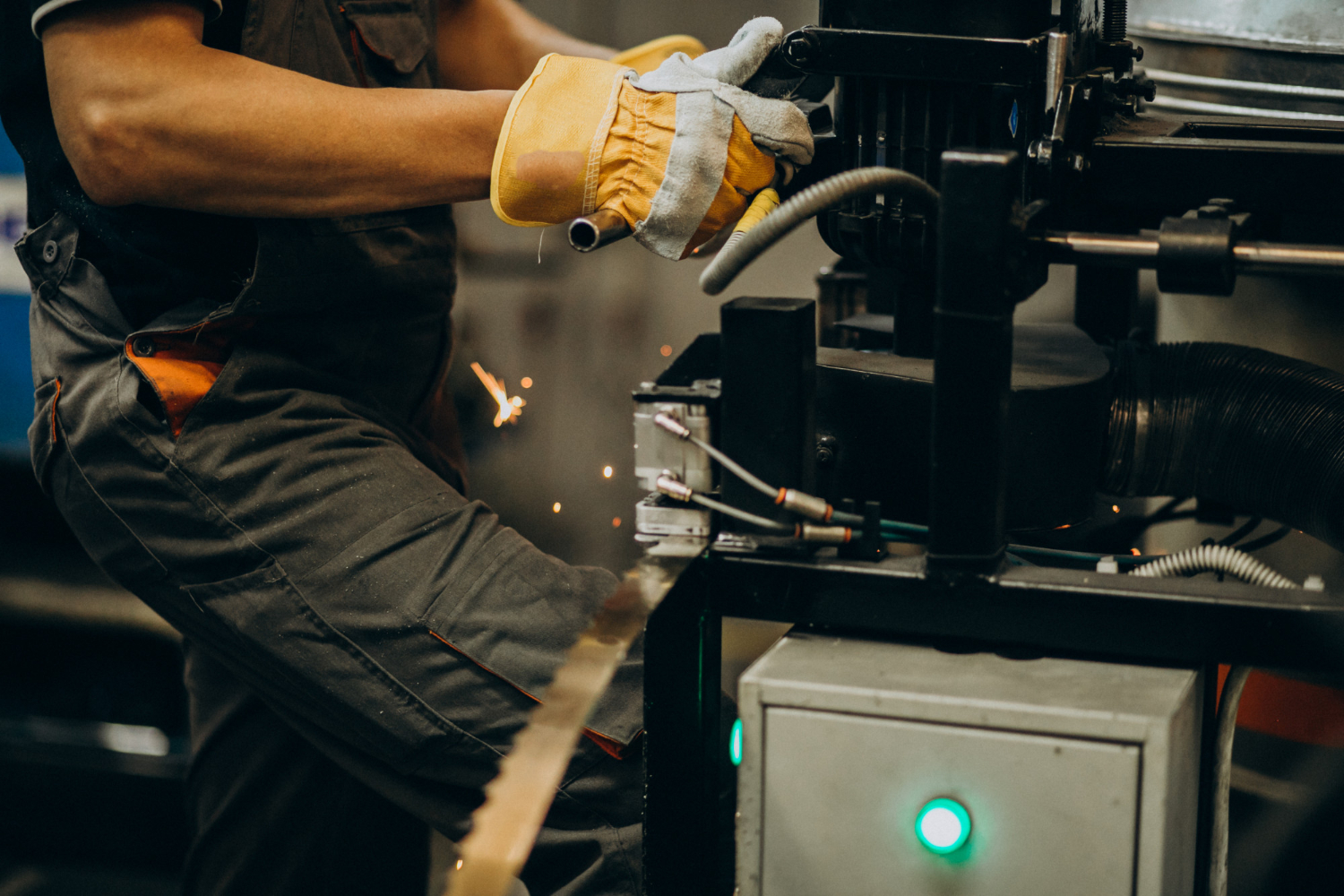
“Given how much it has benefitted us, I would recommend it to anyone.”
Franklin Weenink
Operations Director
Audits: 2 hours saved each time
An environment where safety is so important requires more audits than average. Weenink explains: ‘An audit used to take 2 to 3 hours. Someone had to go into the factory with a stack of papers, tick boxes, take pictures and return to the office to process those papers. Now, the same person walks around with the iPad, ticks boxes and takes pictures in the app, taps ‘send’ and it’s all done. This easily saves us 2 hours per audit.’
It goes without saying that Uzimet meets the essential ISO certificates for quality, health and safety and the environment. Weenink: ‘EZ-GO makes ISO reporting a lot simpler. Everything is recorded in the platform, which makes it easy to demonstrate how things are being done. On top of that, additional employee consultation and participation requirements have been added recently. Since communication is conducted in the app, EZ-GO proves to be an excellent assurance mechanism in that regard.’
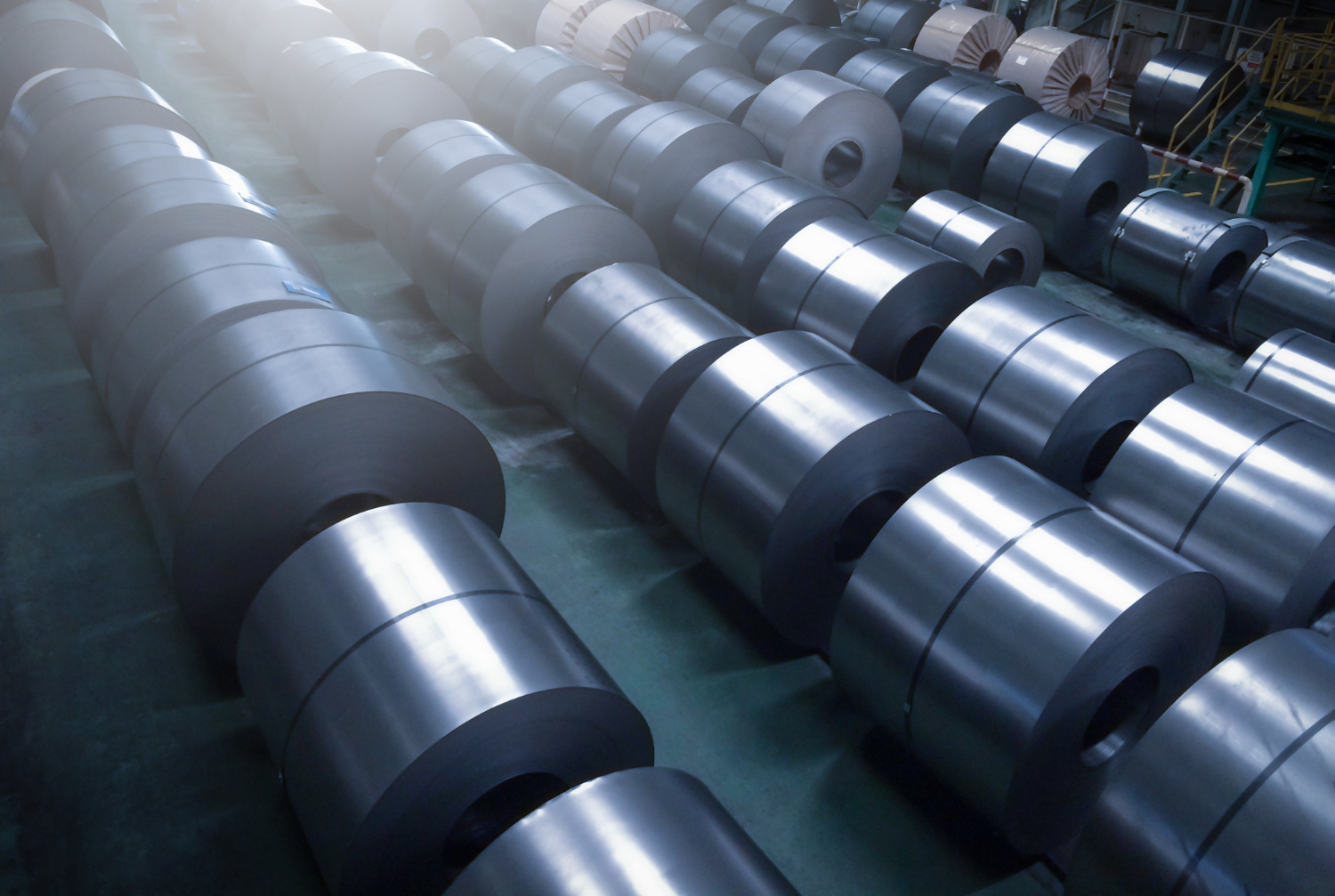
Improved stock management
One interesting application that Soochitsingh has added is the stock checklist. ‘We have 17 high-volume suppliers. I need to update the sales department on the stock numbers for those items every Monday. I used to do this on paper, but now I’m using a checklist in EZ-GO. All I have to do is enter a number for each item, and sales has access to the information right away.’ He smiles: ‘The simple fact that we no longer have to decipher handwriting makes a world of difference. Since the implementation of the app at Uzimet, variations in stock numbers have been significantly reduced.’
He continues: ‘There are so many more possibilities and so many functionalities in the platform that we aren’t using yet and still need to explore. I’m very pleased with the strides we’ve made so far. It simplifies my work as a production leader, internal communication has improved and processes are running more smoothly, both on the factory floor and between departments.’
Faster and better audits
Weenink concludes: ‘We’re currently using the platform in our production environment at Uzimet, but there’s no doubt that simplified and more uniform tasks make any operations more efficient and safer. Financial or services department are certainly no exception to this. The EZ-GO platform provides a structure, which you then populate with your own work instructions, checklists and audits. This means that the platform can be applied anywhere. Given how much it has benefitted us, I would recommend it to anyone.’