When it comes to large-scale technical projects, paper in the workplace can also be a pain-in-the-neck. GEMA Apparatenbouw, which builds 100% on commission, saw EZ-GO as the solution. With the result that project folders have now disappeared from the workplace, leaving welders and builders with more time to do what they do best: welding and building impressive liquid installations.
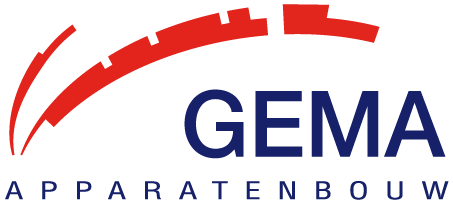
Marco Hollander, controller, and Rudi Puister, business office manager and welding technician, are the driving forces behind the EZ-GO adventure at GEMA. They show how the app can also be of value in a project-oriented environment.
Customised construction
Marco: ‘We build large equipment for the onshore and offshore industry for the transfer of liquids from storage to tankers and ships, or vice versa. We build these installations 100% to order, and they are always client-specific. In the past, we used to create a project folder for each project – one of those folders packed with plans and drawings and checklists that you had to fill in with pen and pencil. Which meant you were carrying these types of folders around a company for 13 weeks; after all, this is how long a project can take. Of course, you sometimes lost your binder, or sheets of paper went into the wrong folder. This was obviously extremely inconvenient and time-consuming.’
‘And all of this going on in an environment where welding and assembly take place, with all the associated dust and dirt. Ultimately, you also then had to retype or scan the manually completed lists to save them digitally. We started to think there had to be a more convenient way of doing things. The ERP system, however, is too complicated and unwieldy for this purpose. On the other hand, EZ-GO has useful templates that you can build on yourself. Which, in turn, ties in perfectly with the ERP system. It all fits together nicely.’
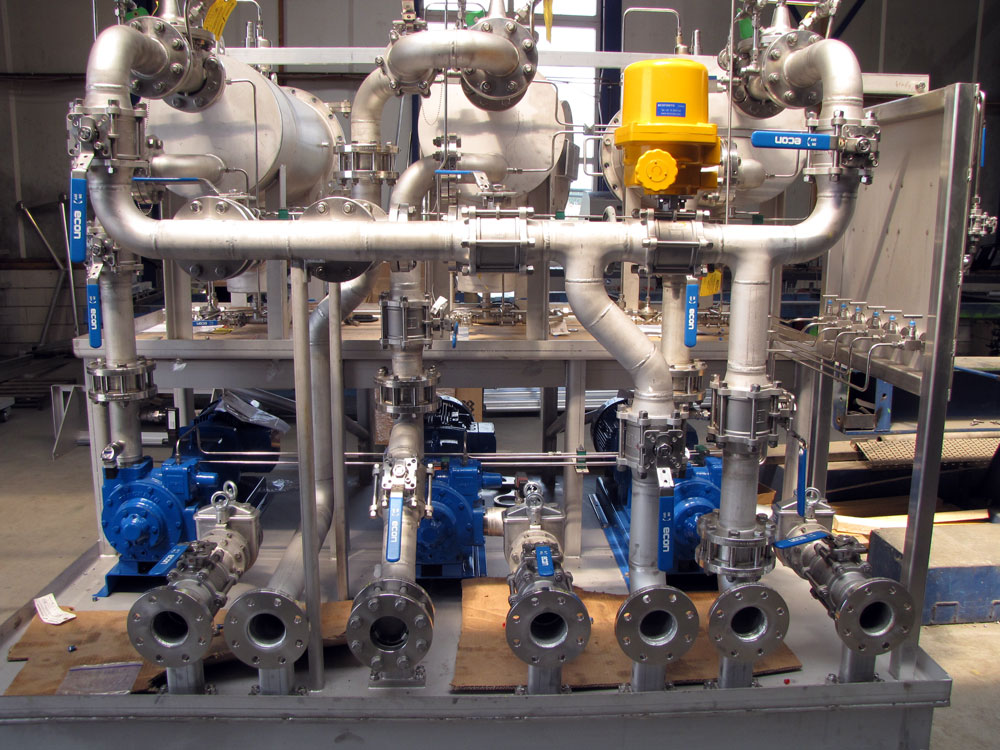
Project management by app
Rudi Puister manages the business office, keeping in touch with project leaders, procurement and work preparation. He explains how they use the EZ-GO app in this project environment. ‘Here we mainly use the app for secondary processes. And not for welding and building. This is done by about 50 experts, so you obviously don’t have to be explaining to them how to do their job. Moreover, there is little staff turnover. We mainly use the app for things like checks and audits. EZ-GO, for example, contains the checklists that go with the projects. The manual lists in those old big folders are therefore a thing of the past. It’s just a matter of retrieving something on the iPad, ticking off the boxes and you’re done. In this way, the status of a project can also be seen in real time. If something isn’t right, an employee can easily create an action for a colleague, add a picture, and then assign it. This saves a lot of time, and is a lot more user-friendly than lugging around folders.’
“If something isn’t right, an employee can easily create an action for a colleague, add a picture, and then assign it. This saves a lot of time, and is a lot more user-friendly than lugging around folders.”
Rudi Puister
Manager Business Office GEMA
Recurring tasks
GEMA also uses EZ-GO for recurring tasks such as cleaning, checking, adjusting and cleaning up. You see the task, perform it and tick it off. For more complicated tasks, there are pictures or videos, and there may also be a PDF of an original machine manual added for reference, for example.
Finally, according to Marco, they do a lot of internal audits with the help of the app: ‘This is mainly about safety checks, which are extra important in an industrial environment like this. Each department performs a weekly audit on a fixed number of safety points, such as fire extinguishers, walkways, power cables, you name it. This is easy to do with EZ-GO, is always complete and is also recorded immediately. Which is handy if an external inspection is coming up. Because you can keep a digital audit forever.’
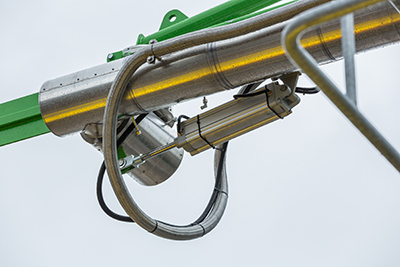
How far along are we?
GEMA started working with EZ-GO in October 2021. ‘In the beginning, things went quite quickly,’ says Rudi. ‘We started with a small department, sat down together and filled the app with the employees. Now we are rolling it out to other departments and activities. It is certainly not my intention to fill in everything. EZ-GO is so great because employees can put in the necessary information themselves. Marco and I mainly have to create the framework and give the employees time for it, for example by giving them a day off now and then from their daily work. Which means it’s done in no time. We expect to be completely finished with implementation by summer 2022.’
Further applications
So, although GEMA is still busy with implementation, they already see follow-up possibilities. Marco: ‘For example, we want to start using the checklists we ourselves use for projects when handing over to the client. I also see possibilities for new applications. With energy prices nowadays, why not make an energy-saving checklist? Everything is possible. That’s because EZ-GO contains basic templates that you can easily set up to meet your own requirements. What’s more, it is easy to change the current lists and tasks if working methods change or if, for example, a new machine is introduced. The possibilities are endless.’