FrieslandCampina has been working with the EZ-GO platform since 2018. A key area where the implementation of the platform has benefited FrieslandCampina, is autonomous maintenance (AM). This is a method that continuously improves the work environment and machines, increases the operators’ and team leaders’ ownership and assures that factory standards are met.
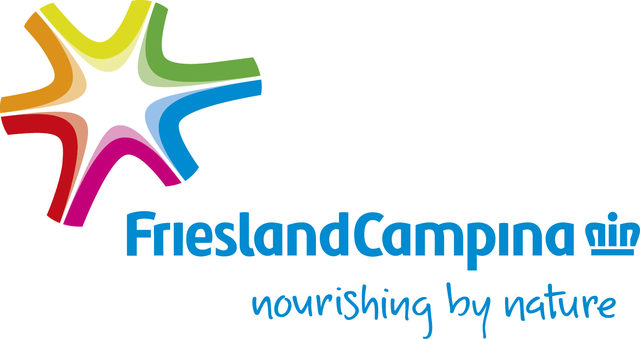
No more hardcopy on the production line
The EZ-GO platform offers an alternative to hardcopy checklists, AM tasks, audit forms and work instructions, which was one of the primary reasons for FrieslandCampina to implement the platform. Operators and team leaders digitize all the documentation themselves. Challako van Gerrevink, Plant manager Leeuwarden: ‘It was all very user-friendly. Within two days we had transferred an entire table’s worth of hardcopy procedures and instructions into the app.’
The company also values the ability to include photos and videos for visualization. Jacob Scheffer, a CI specialist in Leeuwarden: ‘Hardcopy leaves room for interpretation; a photo or video sets a clear, unambiguous standard for everyone.’ The process of onboarding new or temporary workers is simplified: one instructional round with the app quickly and effectively prepares a new operator for their first independent shift.’
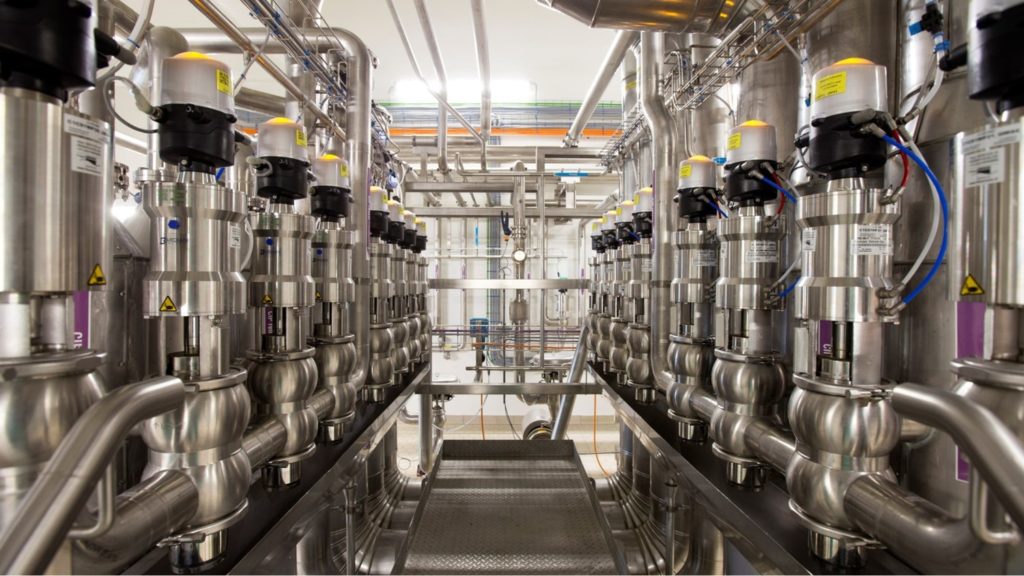
"Conduct the AM project in tandem with the app"
The platform is often implemented together with an AM project. FrieslandCampina Lochem’s CI project manager Hidde Essers said: ‘Cleaning, inspection and other repetitive tasks are now being assisted by the app. The machines are in good shape and are being kept that way because of how the inspections are conducted. This improves our Operational Efficiency.’
He advises to combine the implementation of the app with the improvement of autonomous maintenance. ‘It’s easy to transfer good procedures into the app. But if those aren’t in place yet, it is logical to conduct the AM project in parallel with the implementation of the app. Using hardcopy or T-Cards first would be a waste of time. Enter everything into the EZ-GO app straight away.’
“The EZ-GO app is the enabler of improvement. All I can say is: go, go, go!“
Jacqueline Kerstma
CI-Manager FrieslandCampina Wolvega
Operators and mechanics strengthen each other
An operator can create an ‘action’ in the app, such as an improvement suggestion for the monitoring process or a potential production-related issue. Hidde Essers explains: ‘Mechanics and operators collaborate more closely now. Various maintenance tasks have been transferred to the operators, leaving the mechanics more room to focus on structural maintenance. They communicate more, trust each other more and operators and Technical Services work together to find solutions before problems arise. The app facilitates this.’
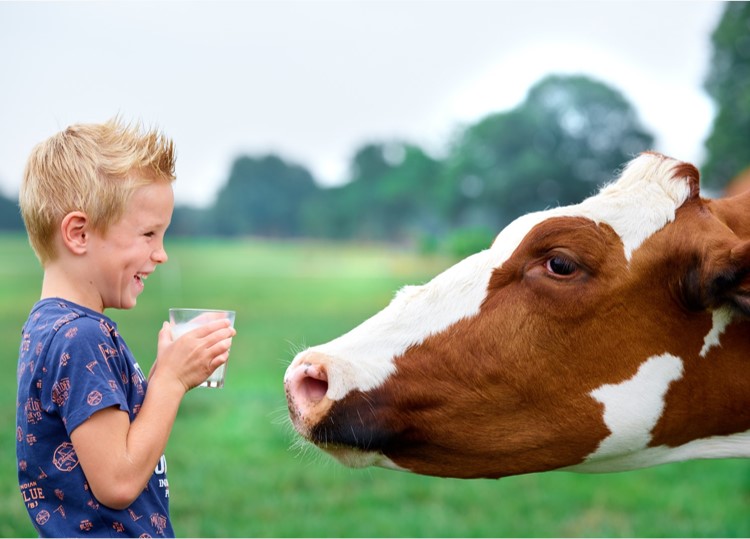
Reports and improvement proposals
The digital app generates overviews and reports that can be discussed in team meetings. A valuable asset, according to CI specialist Scheffer: ‘The statistics reveal points of attention and necessary adjustments, which are discussed in our operator meetings. As a result, our efficiency is improving on a continuous basis.’
Quick rollout
To conclude, we asked CI manager Jacqueline Kerstma from FrieslandCampina Wolvega whether it’s worth it. She couldn’t be more clear: ‘It makes perfect sense and it is very noticeable that the app makes a big difference. It offers overview, the ability to steer, improve the process, safety, quality and efficiency. The EZ-GO app is the enabler of improvement. All I can say is: go, go, go!