Using the EZ-GO platform, margarine manufacturer Upfield wanted to gain increased control over Autonomous Maintenance and respond more quickly to deviations. It turned out there were other benefits too, particularly regarding efficient start-up and machine change overs.
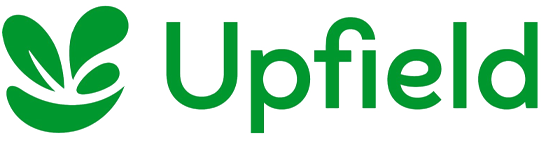
The next step in TPM for Upfield
Process Improvement Manager Ronald Mol is an experienced manager at Upfield and has worked for many years on the professionalization of their processes. ‘In 1997 we launched Total Productive Maintenance. From that time on we let operators do more and more autonomous maintenance tasks. All that time, we did this on paper.’
‘When we were introduced to the EZ-GO digital platform, we saw two major potential benefits: we would be better able to identify and record when tasks have been completed and we would be able to follow up deviations more effectively. And in fact this turns out to work extremely well. Going through and checking off checklists is easy and operators enjoy using them. Following up on deviations is also very effective. When an operator identifies a deviation they pass this on to the support group (Technical Support, Electrical and Instrumentation Services and the Process Improvement Manager). This group then implements measures, potentially together with the operator. The operator receives feedback about the intervention through the app and can then indicate whether the problem has been solved. That makes the app very helpful.’
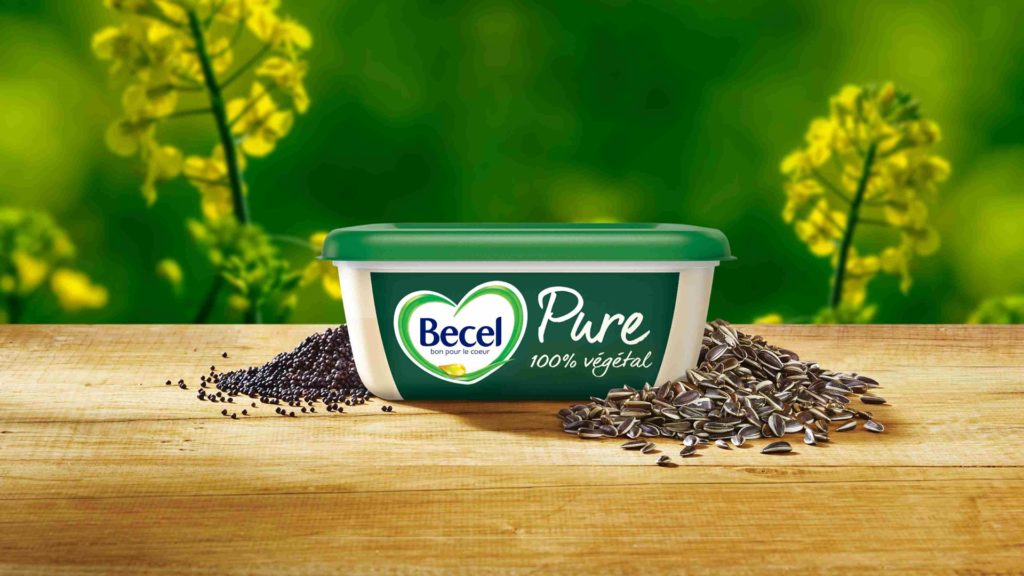
Saving time through clearer processes
Besides checklists, the EZ-GO platform also includes tasks and operating instructions, which operators use for things like starting up and change over machines. ‘Previously, operators would often do this according to their own methods,’ says Mol. ‘We got together and determined what the best procedure was for each task. The app now contains checklists for starting up and change over machines. This renders the methods unambiguous and it limits readjustment to the absolute minimum, saving a lot of time.’
“EZ Factory thinks from the operator’s perspective”
Process Improvement Manager Upfield
Quality Manager Dutch Nutrition
Easy reconfiguration to baseline position
Dutch Nutrition brought in an external consultant to help with implementation: food technology and process engineering specialist Ellen Grashof. “In the beginning, we had more people involved, but it turned out to be more effective for us if one person was focused completely on filling the system, while simultaneously checking to see if our methods were the best they could be,” says De Vries. EZ Factory and implementation partner Pontifexx provide technical and procedural support. “It’s important to have a clear structure from the outset,” Grashof explains. “What is a checklist, what is a task, what do you record. Pontifexx helped us to keep those things in focus.”
Grashof explains that she works closely with the operators and team leaders. “I go out onto the floor and literally stand next to the operator and ask them: show me how you dismantle the filling head or how you replace a gasket. I record every action. I take photos of each step and ask them what could go wrong, what we should pay attention to, and if we could do it better. It’s important for me to take a critical look at the way the work is done with the people who do it, so I can adjust it and the correct procedure can be entered into the EZ-GO platform. Of course, I also coordinate with the team leaders and QA. The next step is making the system better and better by using the improvement circle, because good can always be better. The operators actively use the content in the EZ-GO app and can use the app on the iPad to let us know if a method or photo needs to be adjusted. It helps us work smarter. Every tasks from every department is now available on the EZ-GO platform.”
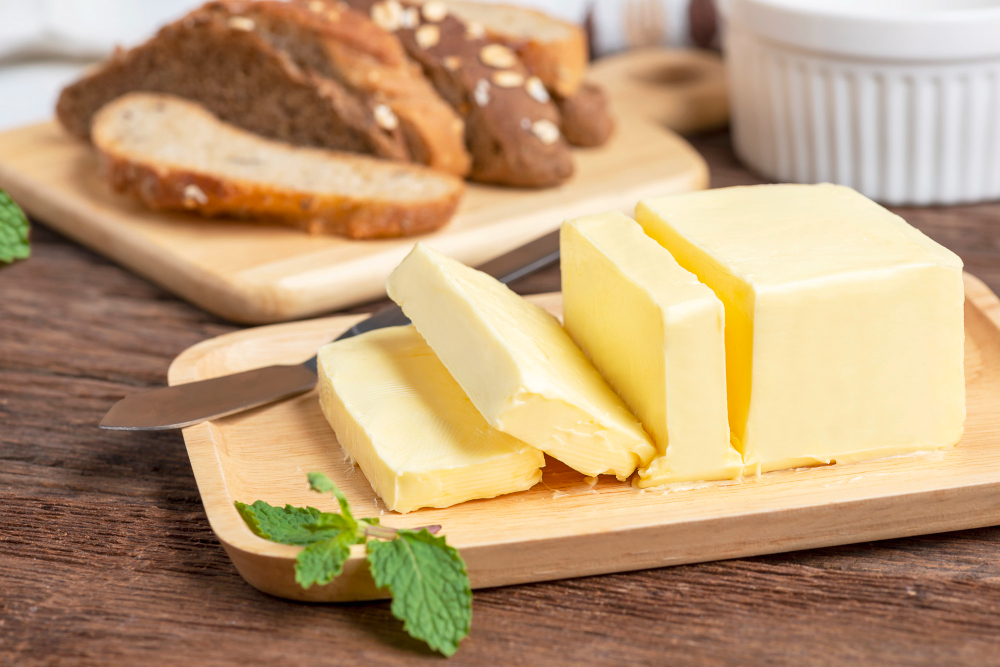
Preventing peaks in maintenance
Upfield was able to transfer most AM tasks directly into EZ-GO. By now, a unit technician always keeps an eye on the lists too. ‘Some checks or steps turn out to be outdated and this is a good opportunity to adjust them,’ says Ronald Mol. In addition, the company made another significant improvement to efficiency. ‘Over time, monthly tasks had become increasingly clustered, causing some weeks to be chock-full of monthly checks. Such peaks cause unnecessary pressure in the workplace. At the same time, you can’t simply spread them out evenly over four weeks; it’s best to perform all tasks that are physically closely related at the same time. EZ Factory helped us by providing an analysis and an improved division of these tasks. That increases stability in the workload and reduces pressure in the workplace.’
Operators improve processes themselves
Upfield is still discovering additional applications and is expanding the implementation of EZ-GO, including for safety and quality audits. For Mol, this makes perfect sense within the objective of constant improvement: ‘The overview that the checklists provide, the clear visual operating instructions, the option to report and follow up problems, as well as the auditing options – all these features combine to give us increased control over the processes and help us improve them, directly in the workplace.’