Confiserie Napoleon is growing and professionalising. That is why they want to digitise work instructions and standards. ‘EZ GO is exactly what we needed.’ The company recognised the benefits of direct and visual communication between shifts. Plus, testing BRC standards, training staff and performing audits would become easier and more effective. And then there were some unexpected benefits, such as those for product development.
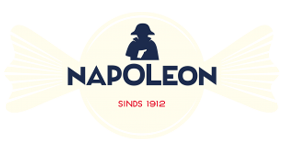
Confiserie Napoleon is a household name: everyone knows their treats, whether it be the round lemon bombs or the ANTA flu throat lozenges. The company has been around since 1912 and underwent a considerable professionalisation process around ten years ago, by recording standards and work agreements. On paper, no less. Little had changed since that time. Except the situation: the company sees new growth opportunities and their workforce is developing. Experienced employees retire, new people join and growth is fuelling an expansion of the workforce.
Reporting and following up on actions
Wim Rutten is floor manager at the Breskens location and responsible for the professionalisation process. ‘EZ-GO is exactly what we needed, because it kills several birds with one stone. Digitisation of checklists and work instructions ensures that tasks are always performed in the same way, that preventive checks are performed consistently and properly registered. In addition, we realised that EZ-GO would help us facilitate communication between shifts: the production manager, technical service and process technologist, for example. If a deviation is noticed during the dayshift, the necessary action can be communicated to another shift via EZ-GO, and the result can be communicated straight back to the dayshift. And vice versa. The photo and video functionality makes reporting, assigning and handling these actions extremely easy and transparent. Because they are entered into a digital system, we no longer depend on verbal, personal transfer of these matters. Problems are solved more quickly and we are able to prevent breakdown or standstill more often.’
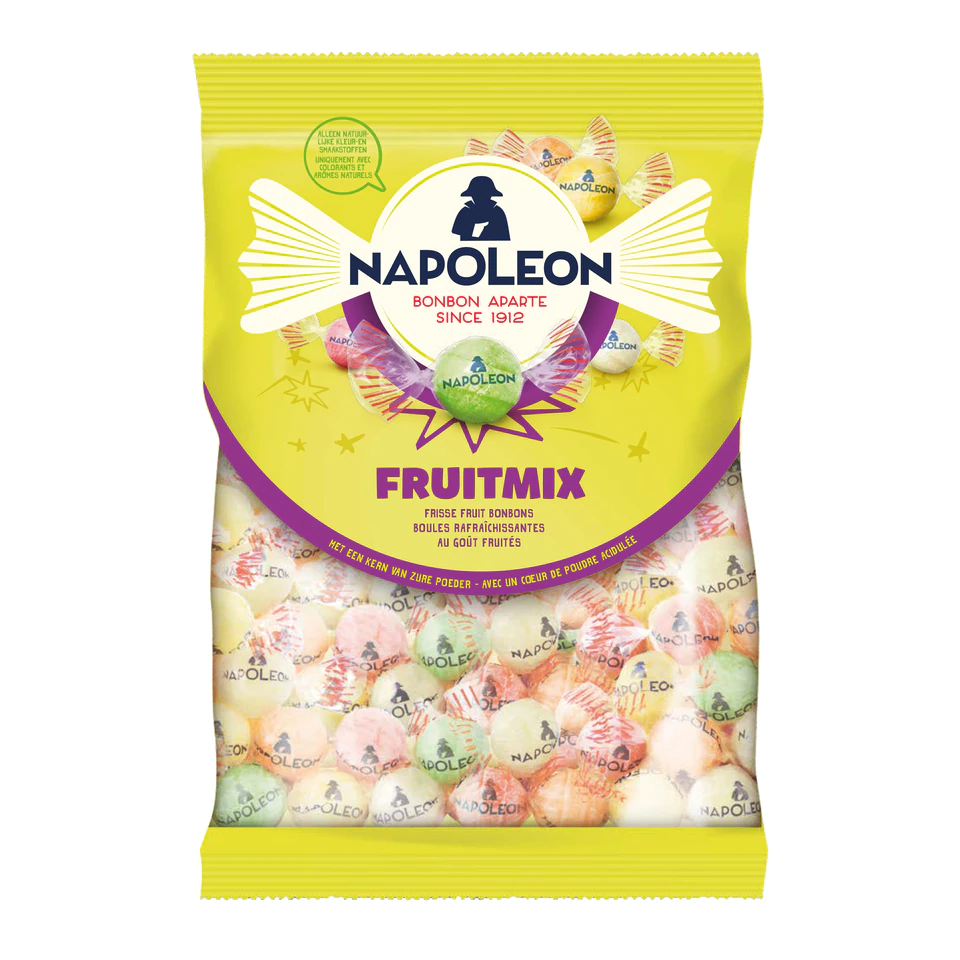
Testing against standards
These were not the only reasons to go for the paperless solution by EZ-GO, which also makes it easier to record your compliance with certain standards. Process technologist Thijs Moorthamer clarifies: ‘It is important that we meet the BRC standards, which means we need to demonstrate that certain things have been done. We could be using paper, but this system makes it a lot faster and easier. Plus, some of our products are halal certified, which means that our cleaning methods are approved by a halal testing organisation. Because our work instructions (one-point lessons) have been recorded into EZ-GO, this testing organisation is able to determine in advance that our production process is halal.’
“Work instructions with photos and videos are clear, unambiguous and great for training new staff.”
Wim Rutten
Floor Manager
Training
The company has a very loyal workforce with a huge amount of experience and knowledge. Some of them will retire in the years ahead. How does one effectively transfer all of that knowledge? Wim Rutten: ‘Once again, EZ-GO proves a perfect solution. Work instructions with photos and videos are clear, unambiguous and great for training new staff. We also use EZ-GO to create tasks for managers, allowing them to test what skills employees possess and what they still need to brush up on.’
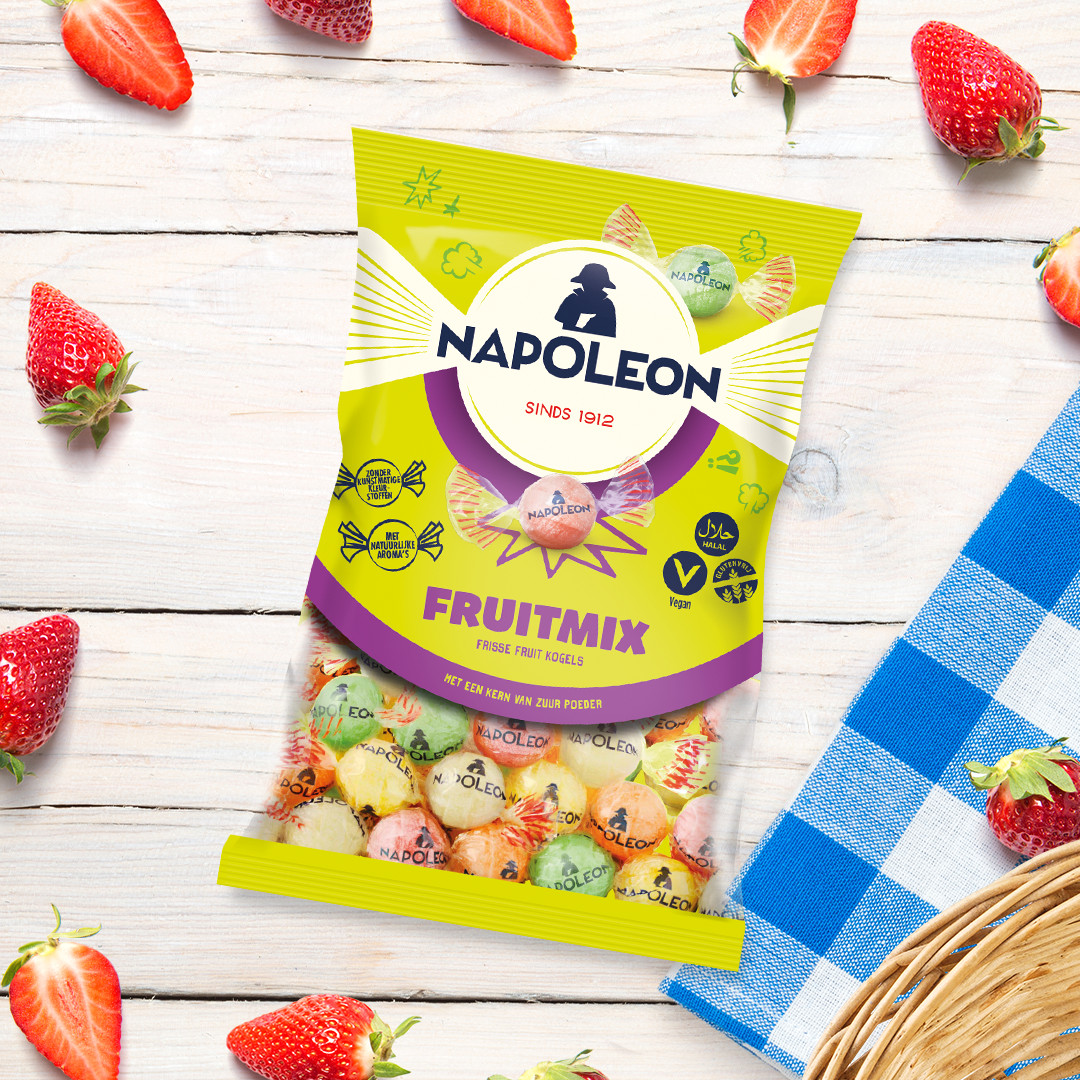
Humble beginnings
Project lead Thijs Moorthamer is responsible for the implementation of EZ-GO. How did they go about it? ‘We kicked off with a small team: myself (quality officer at the time), our production coordinator Patrick Datthijn and another quality officer. Quality and production turned out to be a great combination. Both pay attention to different aspects and someone like Patrick adds thirty years of production experience to the process. First, we tested several functionalities to get to know the system. Next, we created the checklists, tasks and audits for the cleaning activities of one production line. We also used that time to gauge responses from operators. They are mostly practically trained, and we were wondering whether a digital tool like this would catch on. As it turns out, they loved it because of its user-friendliness.’
A one-day implementation
The implementation at Confiserie Napoleon can be roughly divided into two stages, production coordinator Patrick Datthijn explains: ‘First, we updated the content. Many work instructions had not been updated for years, so we tested and updated them all. Plus, we created new photo and video material. Once everything was ready to go, we were able to enter all of the material for the first production line within a day.’ This method turned out to be very effective and was adopted for the implementation of EZ-GO by the other departments too. Thijs Moorthamer gloats: ‘The work instructions and one-point lessons for all five production lines and all four packaging lines, are now all in there.’
Next step: audits
The next major step will be to implement audits. At the moment, it still takes a lot of time to conduct, register and follow up on audits. This is where Thijs Moorthamer expects the most efficiency gains to be made. ‘Once again, we will work in two stages: first, revising the audit and arranging it more logically, e.g. by increasing the distinction between 5S-like tasks and more weighty things that require less frequent auditing. In addition, I expect more time gains because of the fact that audits will be digitally recorded in EZ-GO directly, and actions assigned in real time. No more copy-pasting, uploading photos or mailing actions. This will make a huge difference for Confiserie Napoleon.’
Results
Project sponsor Wim Rutten is content: ‘It’s been six months, and all lines have now been digitised. Actions are being followed up on more reliably, more quickly and communication between production and the technical department has improved. Plus, it shows in the production environment itself: materials are in order and tools are neatly stowed in the right place. In addition to internal communication, communication with our weekly external cleaning service has improved considerably as well: there is now a fixed task list with boxes for them to tick and in the event of any feedback, it is relayed back and forth very conveniently and clearly. One thing we cannot do just yet, is measure whether or not we have reduced malfunction incidence, but I am convinced that we will find just that on the longer term. In addition, I am very pleased that we were able to secure the knowledge of our experienced staff and are training new employees at lightning speed.
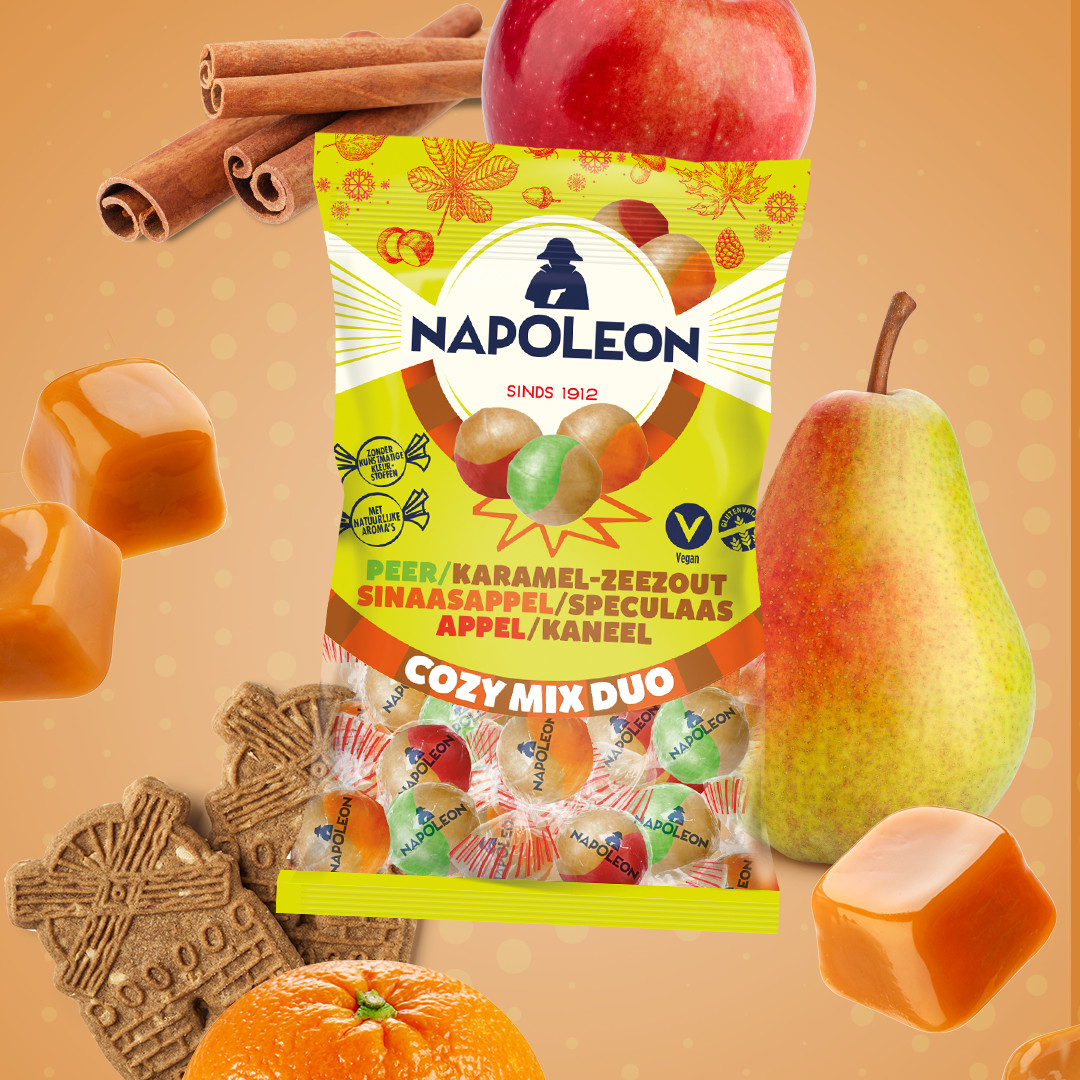
Unexpected additional benefits
EZ-GO delivered several unexpected benefits that turn out to be very important for the candy factory Confiserie Napoleon. Those additional benefits are mainly due to the natural presence of the iPad as a central point of information. Patrick Datthijn: ‘General email notifications are circulated within the company on a regular basis. Some operators don’t check their email very often, which means they used to miss out on important information at times. These news emails can now be read on the same iPad that runs EZ-GO. As it turns out, operators use the iPad to check the notifications on a regular basis.’ As a process technologist, Thijs experiences yet another benefit: ‘In the event of process deviations at night, operators now make videos and photos for me to review the next day. This allows me to make a proper root cause analysis and improve the process.’ Finally, Wim Rutten tells us how product development benefits from the new working method: ‘When developing a process for a new product, we conduct 24-hour test runs. This allows us to see when a product begins to change colour, for example, which means the process needs to be adjusted. Of course, nobody can attend that process for the entire 24-hour cycle. With EZ-GO, we now take a photo every hour, or we make videos that relay the necessary information, allowing us to organise the process with great accuracy.’
In short, the implementation of EZ-GO was a great success, operators are happy with the user-friendly system, task and check execution and recording proceeds consistently and communication has been improved. The desired professionalisation received a considerable boost and Confiserie Napoleon is ready for the expected growth. What will their next product be? That remains a secret for now…